Fitting the Casting to the Foundry
In advising buyers, a topic that often comes up in conversation revolves around the ability to know which foundry is best to produce certain castings. While many foundries may have the capability to make your casting, knowing the ones that provide a “best fit” can shorten your sourcing process. Several key factors are in play to determine best fit: metal type, casting weight and size, annual volume, and part complexity. For best results, the casting sourcing team should make sure the foundry under consideration produces castings that fall within these parameters on a daily basis.
Metal type: Is the casting made from a material that is an industry standard grade or one unique to your organization? If it is a unique material or one the foundry only rarely produces, this could be an indicator there might be potential scheduling problems and increase the part cost. Consider changing your specified material to a commonly cast grade to reduce this problem. Another factor to consider is whether the material type is correct for the application and if there are alternate material selections available. For example, let’s say a steel fabrication is being redesigned as a casting. The designer specifies steel since that was the material used in the original fabrication. However, the part could possibly function just as well in ductile or gray iron, and it is very likely that an iron casting will cost less than a steel casting. The engineering team should be enlisted to help determine if a material change is warranted.
Casting weight and size: Does the casting fit within the weight and size range commonly poured by the foundry? If the casting is on the high or low end of the range, the part may not be a good fit for that foundry. Being on one end of the weight/size spectrum may cause the foundry to require special handling processes that are not in its normal operations, which could cause problems and increase costs. A prime example would be running smaller castings that need to be handled differently through shakeout to prevent the castings from becoming damaged. Similarly, large or heavier castings may need extended cooling times in the mold, and this could add delays when the foundry is producing the casting in an automated process. The need to change standard processes to accommodate your casting is an indicator that your casting may not fit the foundry.
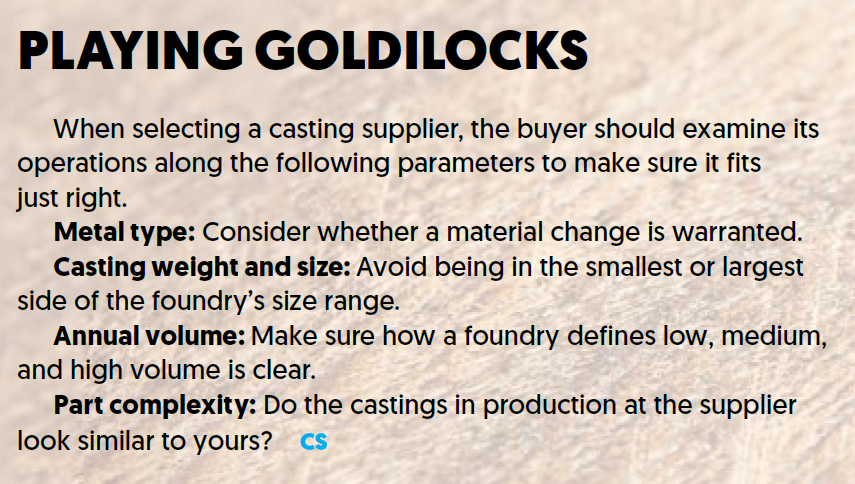
Annual volume: The annual volume of parts you plan on buying needs to fit into the chosen foundry’s lot size range. For instance, if your part has a small volume, it would be wise to choose a foundry that specializes in low-volume/small lot-size casting production. Sourcing a low-volume part at a high-volume foundry will result in increased costs because the foundry’s entire manufacturing process is designed around handling larger lot sizes, and the low volume work just won’t fit well. Keep in mind there can be a large variance between two casting suppliers as to what they characterize as low, medium, and high volume, so it is important that this topic is discussed with any potential casting supplier early in the sourcing discussion.
Part complexity: Determining the proper fit based on part complexity can often be accomplished with a visual comparison during your tour of the foundry. Do you see other production castings that have a similar nature to yours? For instance, if you are looking for a foundry to cast a valve housing that requires complex internal coring, and you see similar castings being produced, you can make the assumption that your casting should fit. The foundry should have all the required knowledge and tools available to produce a conforming part. However, if all you see are simple parts requiring little or no coring, you need to discuss the complexity issue with the foundry management team.
After you have made your assessment, don’t be afraid to ask the foundry if they feel your casting is a good fit for them. This is the proper time for both the buyer and prospective casting supplier to voice their opinions and ask questions to ensure successful results down the road.
Click here to see this story as it appears in the January/February 2020 issue of Casting Source.