Should You Cast It?
Some weldments and assemblies may be money drains for OEMs. Some of those components may be worth considering as castings for possible savings or improved performance.
How do you spot a conversion opportunity for casting? On the floor of manufacturing and assembly operations, countless components are made up of several stamped, wrought or machined metal parts. Engineers often stipulate fabrications and forgings without weighing all their options.
Two questions that should be asked are:
- Could those parts be redesigned into a single cast metal component for improved performance?
- Is there a potential performance gain or cost savings that would make the redesign viable?
The choice of whether a component is best manufactured as welded, assembled, fabricated, forged, machined or cast is based on the component’s geometry, production costs, and requirements in application.
When examining a weldment or assembly for a possible conversion to casting, there are seven considerations to determine the feasibility of the redesign.
1. Geometry
Is the component complex enough to warrant a redesign to casting? This could be a single component that was machined or forged, but more often than not the most impressive cost/weight savings is with a series of stampings and/or other wrought shapes that are welded and/or bolted together.
Components are often designed with the building-block mindset during the prototype stages because of design familiarity. However, the building blocks usually can be streamlined to one-piece cast components.
The types of complex geometry components that make good conversion candidates often have a high surface-area-to-volume ratio. In addition, they usually have long weld lengths that lead to high fabrication costs due to the weld time, materials, and complicated fixtures.
2. Inches of weld
The greater the total weld inches needed to make up a component from several smaller components, the more likely it is to be a candidate for a casting conversion. When a fabricated component has a high number of weld inches in critical stress areas, a greater chance exists that problems in the weld itself or from microstructural effects in the neighboring heat-affected zones will cause failure in the field. High-stress welded joints are generally less capable in overload or cyclic fatigue situations than junctions formed in the metalcasting process.
3. Number of parts
Is the component made up of several smaller parts that have been attached together? If it is, would a single casting reduce the cost associated with part number inventory as well as free up in-house operations for other manufacturing tasks.
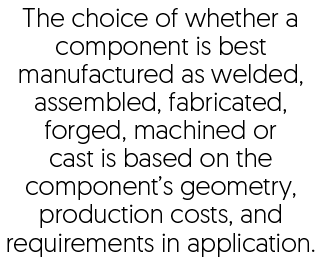
Beyond the inconsistency in mechanical and dimensional properties developed throughout the multi-piece fabrication, the OEM must inventory each part number and absorb the labor costs to manufacture the component.
4. Dimensional consistency
How tight are the tolerances for the component? Is warping ever an issue? The inherent dimensional inconsistency with fabrications is eliminated with a single cast component.
In addition, the in-house manufacturing facility is responsible for ensuring dimensional consistency from part to part.
5. Scrap rates
Are scrap rates high for the component during in-house fabrication? If so, the component may be better manufactured out-of-house via a different production method. The manufacturing facility is also responsible for maintaining a low scrap rate during production, and many of these costs are found in burden rates or are “activity-based” and go unrecognized in a cursory value analysis of component cost.
6. Appearance
Is the component visible? Does it require a clean, streamlined appearance with a fine surface finish? Fabrications offer smooth surfaces, but their welded junctions are not as pleasing to the eye as the continuity of a complex cast shape.
7. Field problems
Does the existing component fail in service? Are the stresses exerted on it too great? Castings provide consistent properties throughout, eliminating much of the variability found in assemblies and weldments. The parameter that unlocks the successful casting design for former fabrications is geometry. Even for castings that don’t serve a meaningful structural purpose, geometry is critical. Geometry for casting design takes into account alloy castability, deflection, stress concentration, risering/gating/venting, and efficient machining and assembly. As a result, well-selected casting geometries are capable of surpassing other methods, particularly fabrications, in making metal shapes that are limited by their process.
Flexibility in geometry choice is more restricted in fabrications, as well as in stamping, forging or machining from stock. Since stress is a function of loads applied and geometry of structure (geometry alone controls the amount of stress for a given system of forces on a structure; material choice controls how much stress is allowable), castings make efficient, cost-effective structures and allow the most freedom of geometry.
In redesigning fabrications to castings, opportunities exist to use casting geometry to simplify design and reduce weight and cost by designing for more uniform stress throughout the part. Since fabrications are made from building blocks of uniform cross-section, they tend to be overdesigned in sections away from the critical stress areas. They also tend to suffer from heat-affected properties and stress concentration factors in the weld joint areas.
The well-known mechanical properties of wrought metals are directional (stronger in the wrought direction, weaker in the transverse direction) and may be compromised significantly by welding. A properly produced high-integrity casting with mechanical properties equal in all directions enjoys uniformity of properties in continuous sections as well as junctions.
Click here to see this story as it appears in the January/February 2020 issue of Casting Source.