Lightweight Steel Foam Plates Have Potential for Military, Civilian Structures
Presently, all steel plates are made by hot rolling continuously cast steel slabs. Investigations carried out at Maynard Steel Casting Company (Milwaukee) have resulted in the invention of lightweight steel foam plates by initially sand casting steel foam slabs and subsequently hot rolling them.
Steel foam plates manufactured using this new process could have a prominent effect on the future direction of steel castings. With the ability to make lightweight steel foam plates in plain carbon and low alloy steels with hardness values ranging from 150-400 BHN, designers could have an entirely new material that never existed before to replace existing components with new components.
This new material could be useful for components for military and civilian structures requiring light weight for fuel economy, energy absorption for blast protection, sound absorption for noise protection, and a wide array of other benefits. The material is also available as a gradient density steel plate with a solid steel surface followed by foam section in the steel plate.
Annual steel castings production in the U.S. is 1 million tons, compared to wrought steel production of 100 million tons. With the ability to make hot rolled steel foam plates using initially sand-cast steel slabs, the invention opens new markets for steel castings.
What is Steel Foam?
The ability to absorb energy of impact or blast is critical to the design of army and navy structures. Steel foam is defined as steel in which pores are deliberately introduced, resulting in a density of at least 20% less than its solid counterpart. Metal foam components display a higher plate bending stiffness than solid metal components. Material properties of steel foams are useful in their high-energy absorption, high strength-to elastic modulus ratios, and high ductility. These structural benefits may potentially be combined with non-structural advantages of steel foam’s low thermal conductivity or high vibration absorption capability in the development of new applications and in the improvement of existing applications for material in armored structures.
Manufacture of steel foam components of a desired density on a consistent basis and on an industrial scale was reported in 2017. Metal foam materials present excellent opportunities for adoption in engineering applications.
Foaming the metal—introducing voids in the microstructure—decreases the density and increases the apparent thickness of the steel. If designed with care, the resulting foamed component can have higher plate bending stiffness and weigh less than solid steel. In addition, the resulting component generally has a greatly increased energy absorption capability and improved vibration, thermal and acoustic properties.
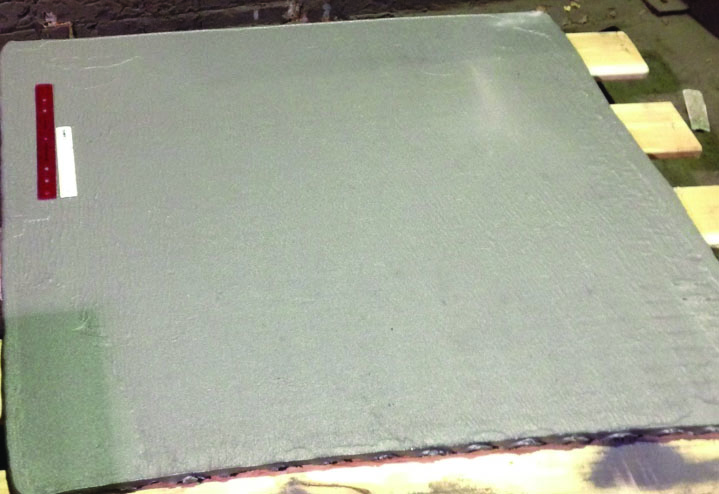
Land-based applications of steel include Abrams tanks, light armored vehicles and up-armored Humvees. Each Abrams tank contains 22 tons of plate, and about 187,000 tons of steel plate were consumed in the production of 8,500 tanks. A light armored vehicle has around eight tons, and about 30,000 tons of steel plate were consumed in the manufacture of light armored vehicles. Sea-based applications include aircraft carriers, submarines, guided missile destroyers, landing platform docks and Nimitz-class aircraft carriers. Aircraft carriers each contain 50,000 tons of steel plate. Submarines typically consume about 5,000 to 10,000 tons of steel plates each. The steel for Nimitz-class aircraft carriers must be able to withstand the impact of a 37-ton F-14 Tomcat aircraft landing on the deck at 150 mph.
Steel foam is steel in which pores are deliberately introduced to reduce the density of the steel and have enhanced properties not achievable with solid steel. In some embodiments of the present invention, manufacturing methods of making steel foam plates include the steps of: providing a 3D-printed sand core bonded with furan nobake binder system, placing the 3D-printed sand core in a sand mold bonded with an ester-cured nobake binder system, providing a suitable gating system for entry of molten steel into the mold, decoring the casting after shakeout, applying an antiscale compound to the surface of the sand cast steel foam slab, hot rolling the steel foam slab, and providing suitable heat treatment after hot rolling to achieve the desirable properties.
Manufacture of steel foam plates with consistently desired densities and predictable properties on an industrial scale with a low-cost conventional sand-casting process and with a subsequent hot rolling operation is a primary feature of this invention. Reduction in thickness from the sand cast steel foam slab up to a factor of 4 has been achieved to date. With the possibility of hot rolling sand cast steel slabs, the problems of casting thin-section steel plates using sand casting processes are eliminated, resulting in the ease of manufacturing large size hot rolled steel foam plates in thin sections up to 5/8 in. Attempts are being made to make even 1/4-in., section steel foam plates.
Advantages of Steel Foam Plates
The manufacture of steel foam plates has been successfully carried out through hot rolling of sand cast steel foam slabs. The process is carried out on an industrial scale with the ability to have consistency in the properties, and to have the potential to replace existing solid steel components with steel foam components used in army, navy, and civilian structures.
The advantages of steel foam plates are:
- Lightweight compared to solid steel, to the extent of minimum reduction in weight of 20%.
- Ability to custom-design the steel foam plate with gradient density, meaning solid surface thickness followed by steel foam section.
- Ability to custom design the metal chemistry and heat treatment to achieve hardnesses in the range of 150-400 BHN and corresponding strengths.
- Ability to provide steel foam plates on an industrial scale with consistent properties.
- Ability to meet any fabrication requirements of existing steel components such as bending, pressing, machining, and welding.
Click here to see this story as it appears in the September/October 2019 issue of MCDP.