From 3D CAD to Casting in Days
The binder jet 3D-printed sand additive manufacturing process is tooling-less, so all the tooling-related design constraints, such as drafts, are eliminated. This gives the design engineer a lot more freedom with feature placements and much higher complexity than the conventional sand casting process. This allows an opportunity for part consolidation, optimization, increased value with reduced lead time, lower overall costs, and tighter dimensional tolerances than conventional sand castings.
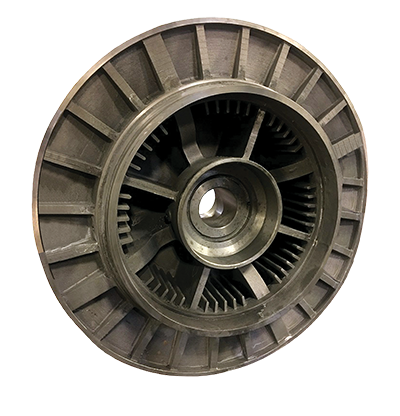
In the case of replacing a large piece of machinery used to manufacture wire, a 3D-printed core embedded into a traditional green sand mold saved the customer $40,000 in tooling. The casting source provider, Dakota Foundry, converted two-dimensional drawings from the 1950s-1960s into a 3D CAD file of a part with intricate features such as cooling fins and wire feed grooves. The part was delivered in days as opposed to the typical eight weeks. CS
See the full column in the March/April 2023 digital edition.